
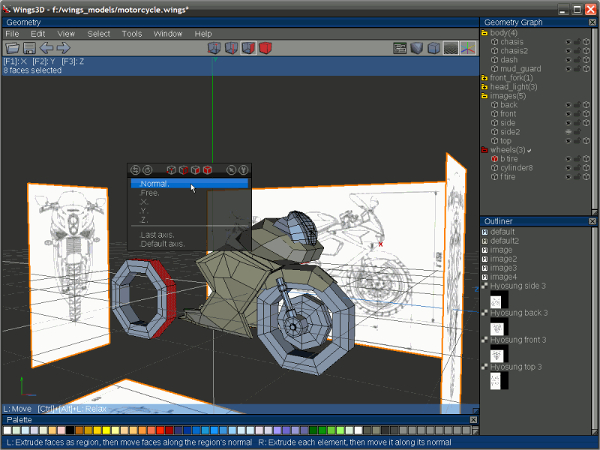
So they developed quad- and eight-core parallel processors which enabled further increases in computing speed. But they reached a limit in fabrication where this was no longer possible. “A decade ago, Intel processors would double their speed every 2-3 years. “The concept of fractal robotics is analogous to the evolution in computer processing,” explains Amolak Badesha, an early investor and strategic advisor at Orbital Composites. Top right, “Hand”: Kuka Titan with 8-10 Orbital coextrusion “Fingers”īottom: Many “Hands” make light work of large composite structures. Top left, “Finger”: Kuka arm with single Orbital Composites coaxial extrusion toolhead. Read “Airbus Ventures Invests in Local Motors to Shake up Aerospace Industry”.) “These were very successful (Note, San Jose, CA, US-based venture capital fund Airbus Ventures has invested $150 million into Local Motors’ 3D printed car technology.
#Target weld in wings 3d series
After a lot of constructive discussion about the printhead design and print materials, Orbital delivered it to CTC in September.”ĬTC used this system to perform a series of very successful tests and make internal presentations, including engineers from the Airbus 3D printing community. “We decided to test their equipment in an Evaluation Phase project, which started in April 2017.
#Target weld in wings 3d how to
“We exchanged ideas on how to improve 3D printing with continuous fiber composites,” says Johannes Born, R&D engineer at CTC and manager of the development program with Orbital Composites. It operates at the forefront of developing composites technology and began working with Orbital Composites in February 2017 after reading an article on its coextrusion printhead. The Composite Technology Center (CTC, Stade, Germany) was originally part of Airbus Stade Research & Technology (R&T) Group, spun off as a subsidiary of Airbus Operations GmbH in 2001 (see my CW Plant Tour article on CTC). This allows the customer to ensure its certifications and feed material supplies. For additive manufacturing to become a dominant process, material prices must be at a minimum.” “Ideally, we design a toolset around the composite materials the customer selects. “We want these coaxial systems to adapt to a wide variety of feed materials,” he says. This is used like an iron to compress the matrix sheath (thermoplastic, thermoset, etc.) into the fiber and smooth the extruded sheath into the previous passes that the tool has made.” The outer region of the nozzle has an extended flat zone surrounding it. “The coextruded composite can be driven into the previous print layer to consolidate and debulk. An annular nozzle around the fiber nozzle extrudes the matrix.

“The central bore in the coaxial extrusion nozzle is the fiber nozzle, rounded to avoid abrading the fiber,” explains Nielsen. Top 10 Considerations When Buying a CNC Machine for Composites Printing in multiple materials, including copper or aluminum wire, nanomaterials and/or conductive inks, to achieve the multifunctional structure desired.Printing fiber coextruded with plastic, ceramic or metal matrix materials including thermosets, thermoplastics and silicon carbide.Printing dry, bindered fiber from 3k to 48k tow.Printing fast - up to 100X faster than current continuous fiber-reinforced plastic technologies.Printing large areas ( rotor blades, aircraft wings, car parts) with high resolution.From there, they deconstructed every part of the conventional fused deposition modeling (FDM) process used to 3D print continuous fiber composites and redesigned it, including new hardware (and software) in order to achieve dramatic new capabilities: “It took over a year just to identify the right questions,” says Nielsen. Based in Silicon Valley, it’s not surprising that he and fellow employees opted for a different approach. From early work building carbon fiber reinforced plastic (CFRP) drones, Orbital Composites CEO Cole Nielsen wanted a better, faster means of manufacturing.
